We first introduced you to this project in our blog Simplifying and Modernizing: Designing a Master Suite and Bathroom Remodel. Our project was then in the design phase, and we gave you glimpses into our process and how we overcome challenges. In this blog, we take the process explanation further to show how energy and symbolism plays a large part in the artistic nature of our work. This article is a natural companion to last week’s blog about our woodshop and how we work closely with our clients to integrate beautiful custom woodwork into their remodeling projects.
The Evolution of a Space
Witnessing a plan come to life is rewarding in itself but when you love what you do the process is often just as fulfilling. The evolution of a space happens not only on a physical level but on an energetic level as well. Spaces hold energy. Energy of the past. Energy of the materials. Energy of the people who create them. Energy of the inhabitants. And when designing homes and personal environments, those energies tend to be more relevant than in public or commercial projects.
Home building and remodeling are not only critically technical, they are decisively creative. And that creative process is often personal and always unique. For me, the beauty in each of our clients lies in their variety. Not only in their individual projects, but also in how they each approach them. Some clients are not concerned with the details and want our team to call the shots, others enjoy getting involved in the process and are curious about the details from start to finish – the rest occupying every variation in between.
The Importance of the Energies and Symbolism of Woods
One of the interesting things about this particular project is when deciding on the wood species of the cabinetry in the master suite, the client (an artist) had an interest in the symbolism and energies of different woods and wanted visual interest in the grain. She brought her research to us and in collaboration with our savvy cabinet builders, a B-Grade, flat sawn walnut was chosen.
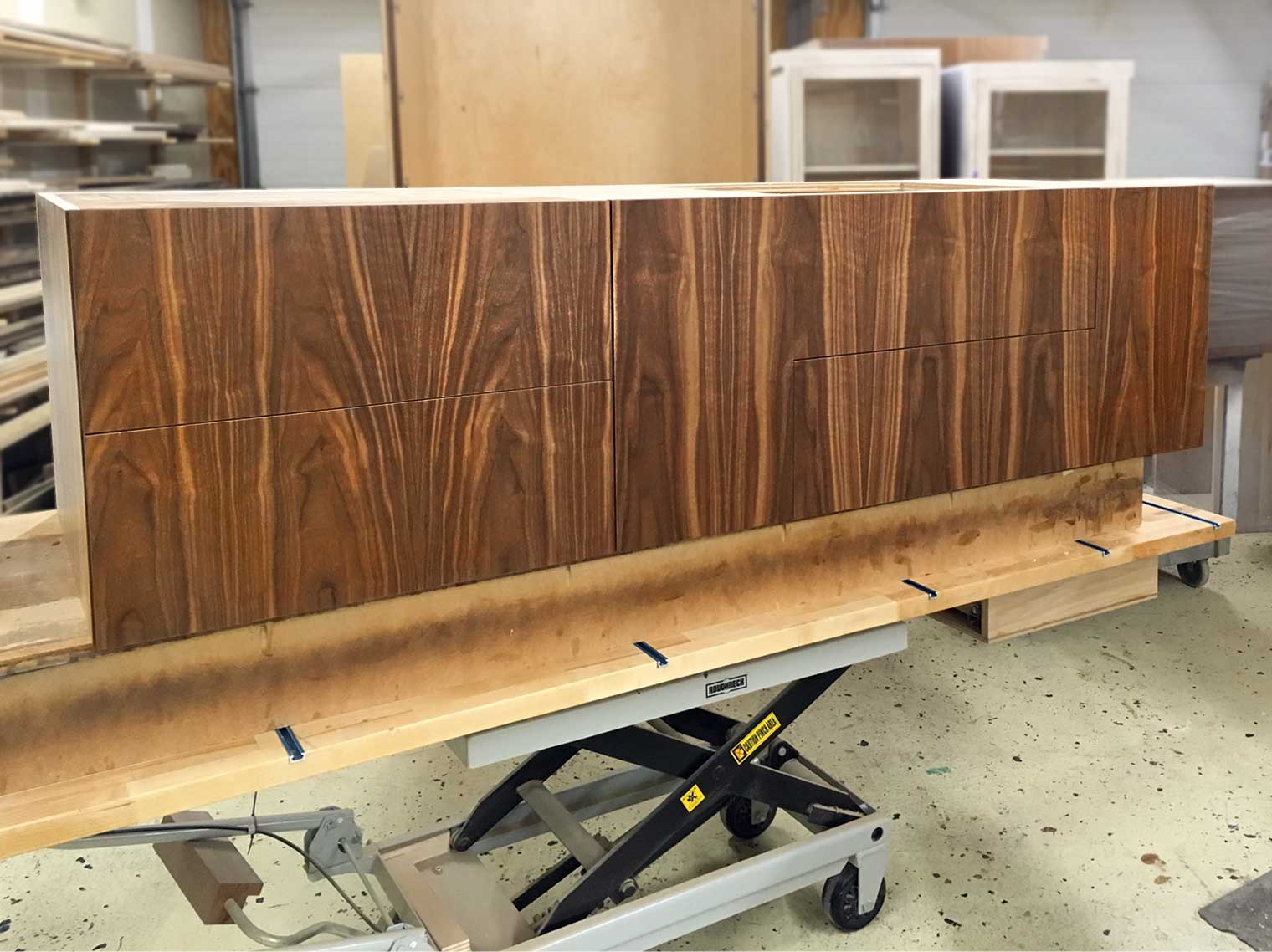
In Progress: Sitting in our shop, ready to be delivered to the site, this is one of three sections of the 10’6” long master vanity.
Native American teachings state that “Walnut teaches clarity and focus, using our mental gifts wisely and how best to use our intelligence.” Regardless of your belief system, one cannot deny the importance of trees in our lives. I’m grateful for the client bringing this to our attention and reminding us of this insight.
As for the more technical lot, it may be of interest to describe the cuts of lumber and how different woods take on such a variety of grain, knots and tones.
The Cut of a Tree – In a Nutshell
When creating various cuts of lumber, there are typically three ways a log is dissected: flat sawn, quarter sawn, rift sawn or rotary-peeled. It is important to keep in mind, the various species, growth rates, the amount of branches, soil types, weather conditions throughout a tree’s maturity, etc. will have an impact on what the cuts ultimately reveal. This diagram will help illustrate.
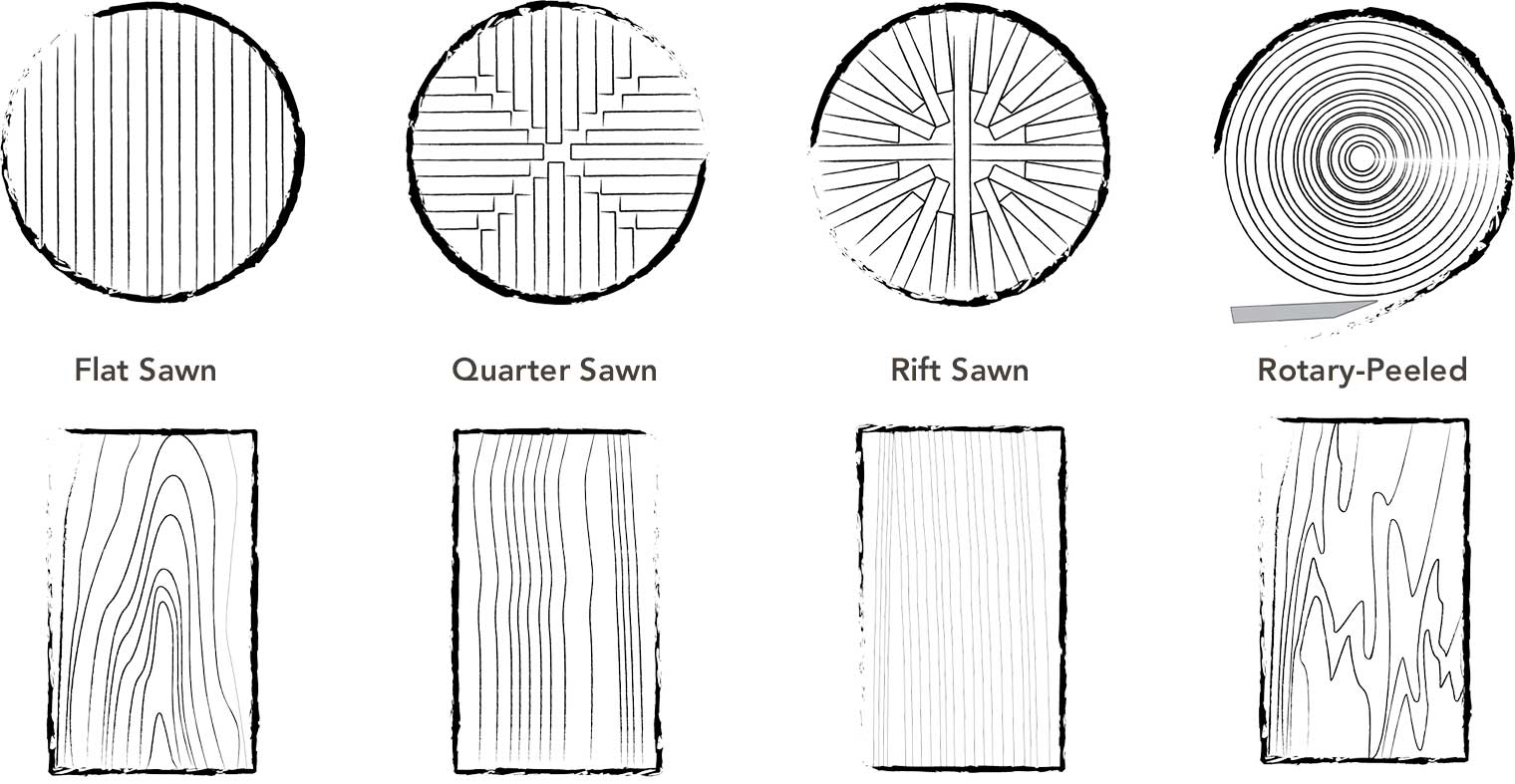
Here are basic explanations of the most common cuts. The more efficient use of the wood, the less expensive.
FLAT SAWN
Because of the simple ‘sliced’ format, this is the most common and economical solid wood cut. It can also have the most variety in grain and tone, depending on the species of tree of course. The closer you get to the center of the trunk the more dramatic the ‘cathedral’ patterns appear.
QUARTER SAWN
As you can see there is more waste in the production and therefore more pricey than flat sawn. Quarter sawn lumber has fairly straight, tighter grain and can have a ‘flecking’ in certain woods like red or white oak.
RIFT SAWN
The least common, most wasteful and therefore the most expensive is rift sawn, although when cut in conjunction with quarter sawn can be a more efficient cut. Rift sawn lumber tends to be more stable and has a unique linear aesthetic with little or no flecking.
ROTARY-PEELED
The rotary peel method is the least expensive, is mostly associated with veneers and tends to resemble the look of plywood. It has the least amount of waste and because it’s cut in thin ‘peels’ it needs backing to give it structure. It is the least stable however and prone to cracking.
Grading Wood – More Schooling
Wood grades are essentially determined by their clarity or level of visual variation. Each species will vary and have their unique range depending on its properties.
Each category is graded from A to D. A being the clearest and D having the most defects or character.
- A Grade: Clear cut with no knots. Usually a tighter, straighter grain.
- B Grade: Contains a few defects and at times will have a stronger ‘cathedral’ pattern.
- C Grade: Some small knots. Again, this varies depending on the species. A clear, A Grade Alder may have some small knots due to its distinct character.
- D Grade: A few larger knots and defects. Usually rough sawn and is less stable
Scratching the Surface on Veneers
Veneers can be made using any of the above cuts and are the most eco-friendly way to get that ‘wood look’. A veneered wood core mainly consists of recycled waste from standard mill production (sawdust, etc.) and uses a thin veneer of the actual wood. The thicker the veneer, the thicker the durability.
Back to the job site and back to work on the master suite. Be on the lookout for a follow-up “Project in Progress” blog coming up. In the meantime, see our other master suite projects in our Project Gallery.